In their quest to deliver more oil and gas from increasingly remote and complex reservoirs, drillers are turning to extended-reach drilling (ERD) methods to directionally drill miles-long laterals from a single vertical wellbore.
Not only do these methods require drillers to fundamentally change their well-construction strategies, they have also put greater pressure on service companies to provide tools and services that allow the well to reach target depth safely, efficiently, and cost effectively. Cable Protection For Extended Reach Wells
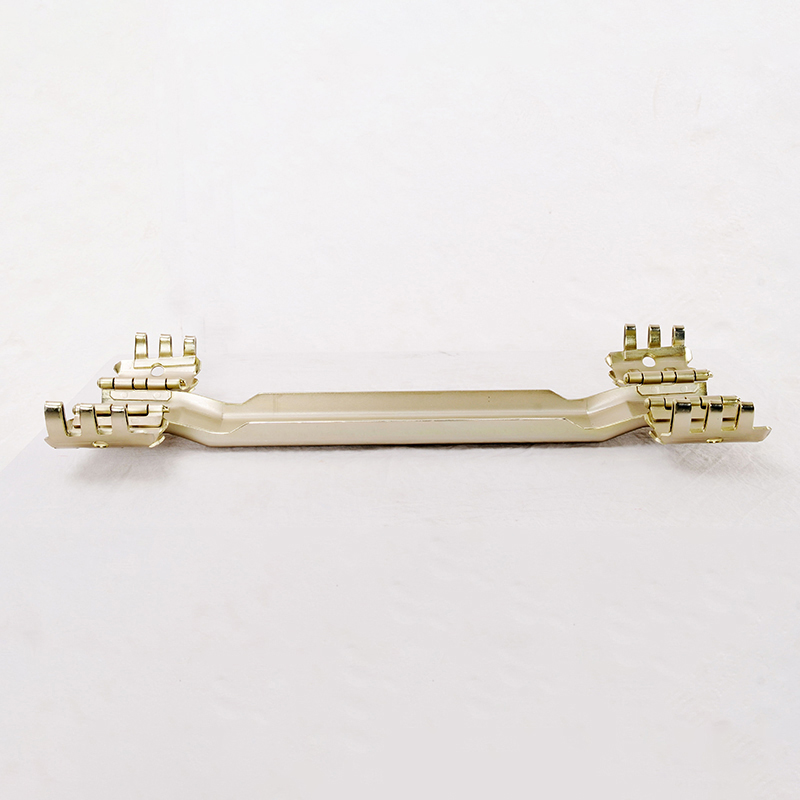
Extended-reach well construction presents many challenges during drilling operations, particularly high torsion, friction, and compression issues during casing installation. These challenges increase significantly while drilling ultra-extended reach laterals (those with measured distances of 25,000 ft [7,620 m] or greater) in offshore environments, as one major operator experienced while attempting to drill a record-setting ERD well off the coast of California.
The operator's primary objective was to safely run a 95⁄8-in. liner, in one trip, prior to entering the pay section. The operation would require making up, rotating, and pushing more than 27,000 ft (8,230 m) of liner into a 12¼-in. ERD well section with deviations up to 84°. Additional objectives included monitoring torque of the casing during makeup and reaming operations, maximizing operational efficiency between rig-down of casing running and rig-up for setting the liner on drill pipe.
Ensuring that this length of casing string could be successfully installed, with gas-tight-connections and sound mechanical barriers, had rarely been accomplished at this distance. The conventional approach to running casing in ERD wells, which calls for the lateral to be completely filled with drilling fluid during running, typically introduces high frictional forces between the casing string and the wellbore that must be overcome to reach planned depth. In the event that the casing gets stuck in the horizontal section, the only option has been to pick up the string and reciprocate it, while hoping that the weight of the string is sufficient to force it through the obstruction and allow running to continue.
As an alternative, the operator planned to implement a floating technique for casing string installation, in which the drilling fluid is replaced with entrapped air in the horizontal section. This practice significantly decreases the frictional effects during deployment, and makes the overall casing string buoyant. To provide greater assurance that the string would be efficiently delivered to total depth through the long horizontal step out, top-drive casing running tools were deployed.
These tools, which attach to a rig's top drive and combine many conventional casing tools into one system, allow the top drive to safely and efficiently handle casing installation. This extends the top drive's range of functionality by enabling simultaneous rotation, reciprocation or push down, and circulation of the casing string. The addition of a reaming shoe or drillable casing bit opens up the possibilities of reaming in a pre-drilled section, or extending through problem zones or drilling complete hole sections – all with the casing string.
Since their introduction for land rigs in the 1990s, top-drive casing running systems have evolved to accommodate a broader range of applications, including offshore rig deployments of casing sizes up to 22 in. with up to 750 tons of hoisting capacity and 80,000 ft-lbs of torque. To date, thousands of casing strings have been run or reamed using a top-drive system and over 2,000 problem zones or well sections have been successfully drilled with casing strings.
While these capabilities gave the operator confidence that the system could help deliver their ultra extended-reach casing string to total depth, there were several additional risks that had to be carefully addressed while floating the string. These risks included handling a buoyant casing string, potentially collapsing the casing by rotating at the same depth for extended periods (and generating heat-related stresses), or being forced to reciprocate the casing or pull out of the hole due to excessive cuttings build up. Reciprocation or pulling casing were considered far too risky beyond certain depths, as the generated swab pressures could have caused a kick, mud loss or hole collapse.
The operator realized that effectively managing these risks required more than a purely technical solution. It must be coupled with a greater understanding of the entire well-construction process if total depth is to be reached at the required level of safety, speed and cost.
Weatherford also realized that a focus on making connections at the rotary alone was limiting, and that greater synergies between casing running and other well construction operations existed. Many operator problems could be better addressed by looking at the full scope of the operational objectives and challenges to develop a comprehensive technical program for building the well or well section.
Using an all-encompassing well-construction program, the company shifted the conversation from simply running casing to working with an operator in the early stages of the project to understand all the challenges they face in delivering a high-integrity casing string to total depth.
By combining several well-construction services and engineering resources into one comprehensive offering, the correct fit-for-purpose well-construction plan can be developed and implemented in the well planning phase to reduce non-productive time (NPT), increase efficiency and optimize well design.
This approach had already proven successful in helping operators overcome many critical issues across the globe prior to this application:
•Poor cement placement:An operator in the Caspian Sea experienced total mud losses, poor cement placement, and zonal communication. The combined application of a top drive casing running system, a rotating/hoisting cement head and special rigid centralizers solved the problem by minimizing time between casing running and cementing operations, and full casing string rotation and reciprocation during cementation.
•Caving in top-hole section: In Australia, severe underwater currents and poor visibility made it difficult to locate the pilot hole after conventional drilling of the surface hole section. Additionally, soft, caving formations made it difficult to get casing to planned depth. Application of a top drive casing running system, special rigid centralizers, and drillable casing bit enabled the operator to simultaneously drill and case the hole section in one trip.
•Depleted and over-pressure zones: A deepwater GoM operator needed to drill through and set casing over a pressured shale and a subsequent depleted sand within one hole section which, with conventional methods, would most likely require two strings of casing to achieve. The well plan would not allow use of multiple strings, slimming the wellbore. The liner was reamed and drilled through the pressured shale and depleted sand with no mud losses using a high torque liner system, rigid centralizers, and a drillable casing bit.
The ability to meet project objectives in the offshore California job was also enhanced by close collaboration on many fronts.
This collaboration with the operator began on previous ERD wells, run both in California and outside the US. While the previous wells did not incorporate laterals nearly as long as this well (earlier well laterals ranged from 15,000 to 18,000 ft (4,572 to 5,486 m), success in achieving TD gave the client confidence in the service, as well as a familiarity with the offering that promised to improve operational efficiency.
The operator/service provider relationship also extended into the torque and drag modeling stage, in which the operator's data acquired from previous ERD wells, was applied to the current well and subsequently used to design a specific technical solution for this well section. Service engineers thoroughly analyzed the torque and drag modeling results, which indicated that the equipment would need to withstand the torque necessary to rotate and push the entire 95⁄8-in. liner through the lateral to total depth.
The service provider's field operations and engineering teams also worked closely together to ensure an efficient transition from running casing to running the liner on drill pipe. This transition had to be executed as quickly as possible to minimize the static time for the casing string in the well and likelihood that the liner could get stuck. Therefore, a trial rig-down of the casing running system and drill string rig-up was performed on the rig site prior to the job to familiarize field personnel with the process and become as efficient as possible.
This full-scope collaborative approach to reaching target depth allowed the operator to successfully run the casing string to planned depth – on the first run – and achieve a world depth record for a fixed-platform ERD well.
The combination of the top drive casing running and large bore, high torque liner systems was used to successfully make up, float, push negative weight, and rotate the entire casing string to 27,255 ft (8,307 m). The casing-running and liner system's torque capacity of 68,000 ft-lbs was more than adequate for the project as actual rotating torque never exceeded 22,000 ft-lbs.
A special hydraulic liner running tool was mechanically locked to the top of the hanger and able to rotate the liner in compression, tension or neutral without fear of prematurely dropping the liner. A specialized hydraulic "grapple" gripping system was employed in the casing running system that creates 60 metric tons of "pre-loaded" gripping force, allowing top drive weight to be applied with simultaneous push down and rotation of the casing string. Because the casing running system was remotely operated, the need for a stabber in the derrick and manual handling of power tongs on the rig floor was eliminated, providing significant safety enhancements in the process. In addition, a torque-turn monitoring system and electronic load cell incorporated in the system helped ensure that each connection was made to the specified torque for casing string integrity and the reaming torque was accurately monitored during reaming.
The system was used continuously for 83 hrs with no technical problems, and achieved run rates of up to 17 joints per hour. Ultimately, this service helped the operator reach target depth in this ultra ERD well, with no safety or environmental incidents, 92 days ahead of plan.
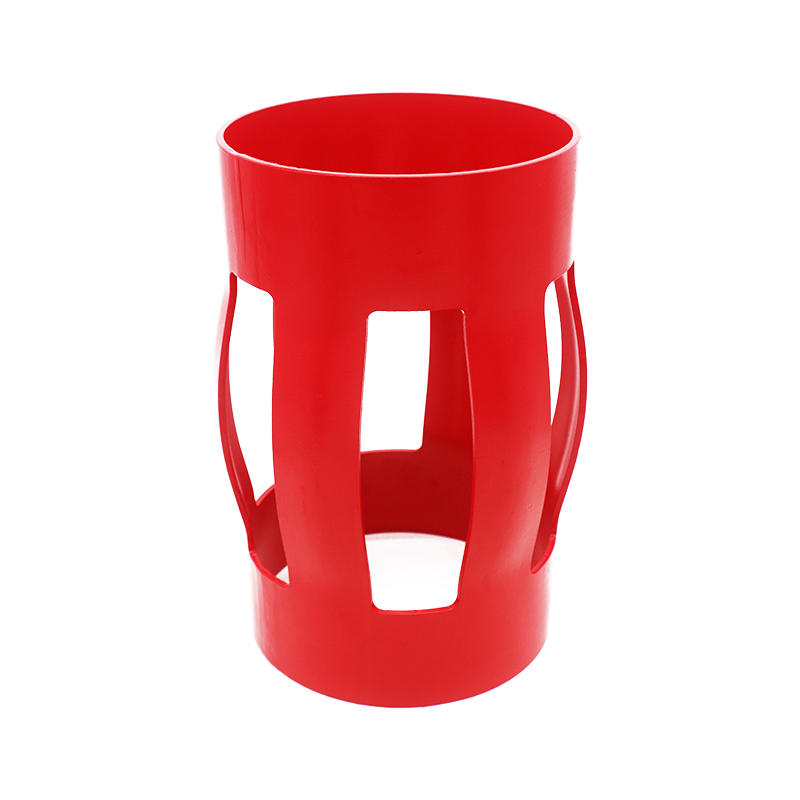
Positive Centralizer The transition from providing top-drive casing running tools to offering a comprehensive well-construction service – encompassing several interrelated competencies – is a natural progression that highlights how the operator/service provider work relationship is evolving. In the future, this comprehensive approach promises to not only safely and efficiently deliver ever-longer laterals, but also may find application beyond well construction to optimize production and extend a reservoir's productive life.