This custom drilling and annular cutting machine makes aluminum parts for a construction-industry brake. It features a single drillhead (orange frame) that travels 16 feet at speeds of up to 2 fps. Photo courtesy Lumco Manufacturing Co.
The RPS features a pinion consisting of 10 or 12 needlebearing supported rollers that engage a rack tooth profile. Photo courtesy Nexen Group Inc. 3D Fence Welded Mesh Machine
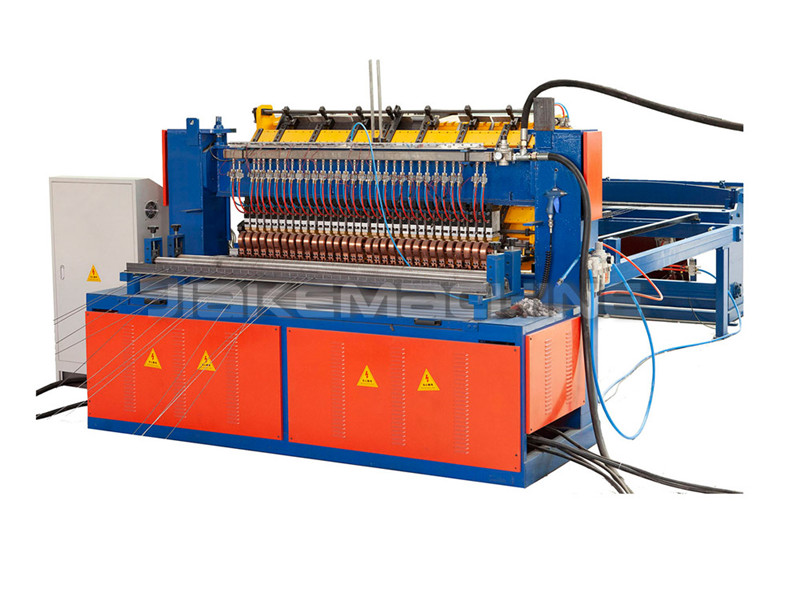
Ask a random group of people to explain Rotabroach annular cutting, and you’ll probably get silence. Pose the same question to workers at Lum, MI-based Lumco Manufacturing Co. and you’ll get an earful. The reason: They often make machines that use this technology to cut ferrous and nonferrous metals.
Invented by Dr. E. Douglas Hougen in the early 1970s, the Rotabroach annular cutter is a hollow, multiple-edge tool that cuts only an annular groove at the periphery of a hole, leaving a solid core or slug at the hole center. The cutter creates cylindrical holes in a circular cross section faster, easier, and more accurately and cost-effectively than conventional twist drills or drill bits.
Recently, Lumco built a custom drilling and annular cutting machine that a customer uses to make aluminum parts for a construction-industry brake. The machine features a transversing drillhead that travels 16 feet (at speeds of up to 2 fps) and stops at multiple stations to drill and cut parts from aluminum sheets 7 feet, 3 inches, to 14 feet, 6 inches long. Sheets are manually loaded, and parts are automatically unloaded from the machine, which is programmed to handle 21 part configurations.
The biggest challenge Lumco engineers faced while designing the machine was finding a linear motion system that meets two criteria: it easily integrates with the machine, and it is powerful enough to move the drillhead through a large amount of aluminum chips that collect at the bottom of the machine.
Lumco engineers carefully considered three traditional types of linear motion systems before rejecting all of them. The ballscrew wasn’t feasible due to the length of travel needed, and belt drive actuation lacked the necessary accuracy. As for using a standard rack-and-pinion system, they felt it could handle the distance and speed, but produced too much backlash and wear.
The engineers then reached out to linear motion control specialist Nexen Group Inc. for help. Nexen suggested Lumco use Nexen’s RPS roller pinion system, noting its speed capability of 36 fps and accuracy to within ±0.00118 inch. After considering the drillhead’s speed, weight and accuracy requirements, Lumco decided to go with the RPS.
“The system [provides] us all the accuracy and speed of a ballscrew at any length of travel we need, and [it] gives us more options to package servo axes,” explains Mike Morris, president of Lumco. “We’re no longer dependent on the traditional ballscrew approach, which limited the length and speed of [our] machine design. Most importantly, our customer is very happy with the machine performance.”
Unlike the traditional rack and pinion system, the RPS features a pinion consisting of 10 or 12 needle-bearing supported rollers that engage a rack tooth profile. The sealed and lubricated rollers move smoothly along the profile, resulting in zero backlash and 99 percent efficient rotary-to-linear-motion conversion. The tooth profile is lubricated with a high-performance light grease at installation and then every six months or 2 million pinion revolutions.
For more information on linear motion control products, call 800-843-7445 or visit www.nexengroup.com/nxn.
Jim is a senior editor of ASSEMBLY and has more than 30 years of editorial experience. Before joining ASSEMBLY, Camillo was the editor of PM Engineer, Association for Facilities Engineering Journal and Milling Journal. Jim has an English degree from DePaul University.
You must have JavaScript enabled to enjoy a limited number of articles over the next 30 days.
Connecting shop floor tools to a manufacturing execution system is critical to error-proofing assembly processes, improving quality control, and lowering defect and scrap rates. Join Torrence Williams, Partnerships Manager for Pico MES, and Dan Smith, VP of Sales for Kolver Tools, as they discuss an easier path for manufacturers to start connecting their factory floor.
This topic is something that challenges each of us every day that we go to work. This talk is about change and why it works and why it fails. It is focused on manufacturing facilities, because that is where the author has spent most of his working life.
Copyright ©2023. All Rights Reserved BNP Media.
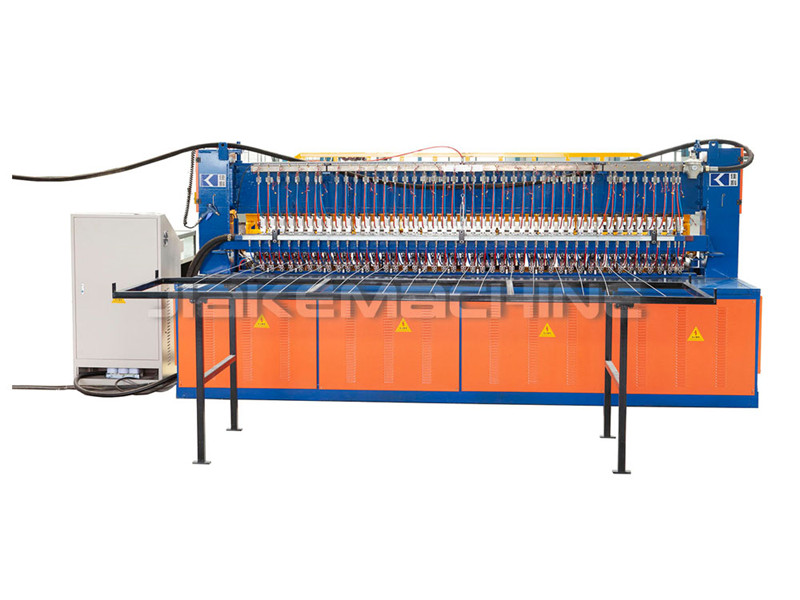
Hexagonal Wire Netting Machine Design, CMS, Hosting & Web Development :: ePublishing