Lithium carbonate regenerated from recycled battery waste using a patented process developed by RecycLiCo has successfully been qualified by C4V’s Phase 1 Supply Chain Qualification program through testing in battery cells. In other words: C4V has confirmed that recycled lithium’s quality rivals that of “virgin” lithium.
“As demand for lithium soars, it’s becoming increasingly clear that mining alone cannot sustainably meet global needs,” explains Zarko Meseldzija, CEO and Director of RecycLiCo. “This test confirms that our recycled lithium is not just a viable alternative, but we believe it will soon be considered more valuable than mined lithium.” Battery Test Bench

The qualification program conducted by New York-based C4V, a lithium-ion battery technology company that creates next-generation storage materials suitable for Gigafactory-scale solutions, has yielded exceptional test results. Utilizing RecycLiCo’s patented processes, lithium carbonate is extracted from battery trash and transformed into cathode material before being integrated into battery cells. The battery cell tested showed high capacity and stability throughout the cycle testing, and C4V’s exacting standards demonstrated that RecycLiCo’s recycled lithium is on par with mined, “virgin” lithium, putting the company “at the forefront of manufacturing sustainable battery materials,” according to its latest press release.
C4V also qualified the RecycLiCo NMC811 precursor cathode active material (“pCAM”) in cell production and performance evaluations. RecycLiCo’s lithium carbonate and pCAM will next undergo phase 2 testing, which will focus on producing both “pouch” cells and commercial-sized prismatic cells.
“We are pleased to announce the successful qualification of lithium carbonate in Phase 1 process,” commented Baasit Ali, Engineering Manager, Supply Chain of C4V. “As being the key component in (the) battery value chain, this milestone underscores our unwavering commitment to driving sustainable solutions and the industry forward.”
In response, Meseldzija emphasizes the broader Recyclico vision. “Securing this validation drives us towards a future where our closed-loop process not only recycles but revolutionizes battery production, supporting a fully integrated, on-site battery lifecycle.”
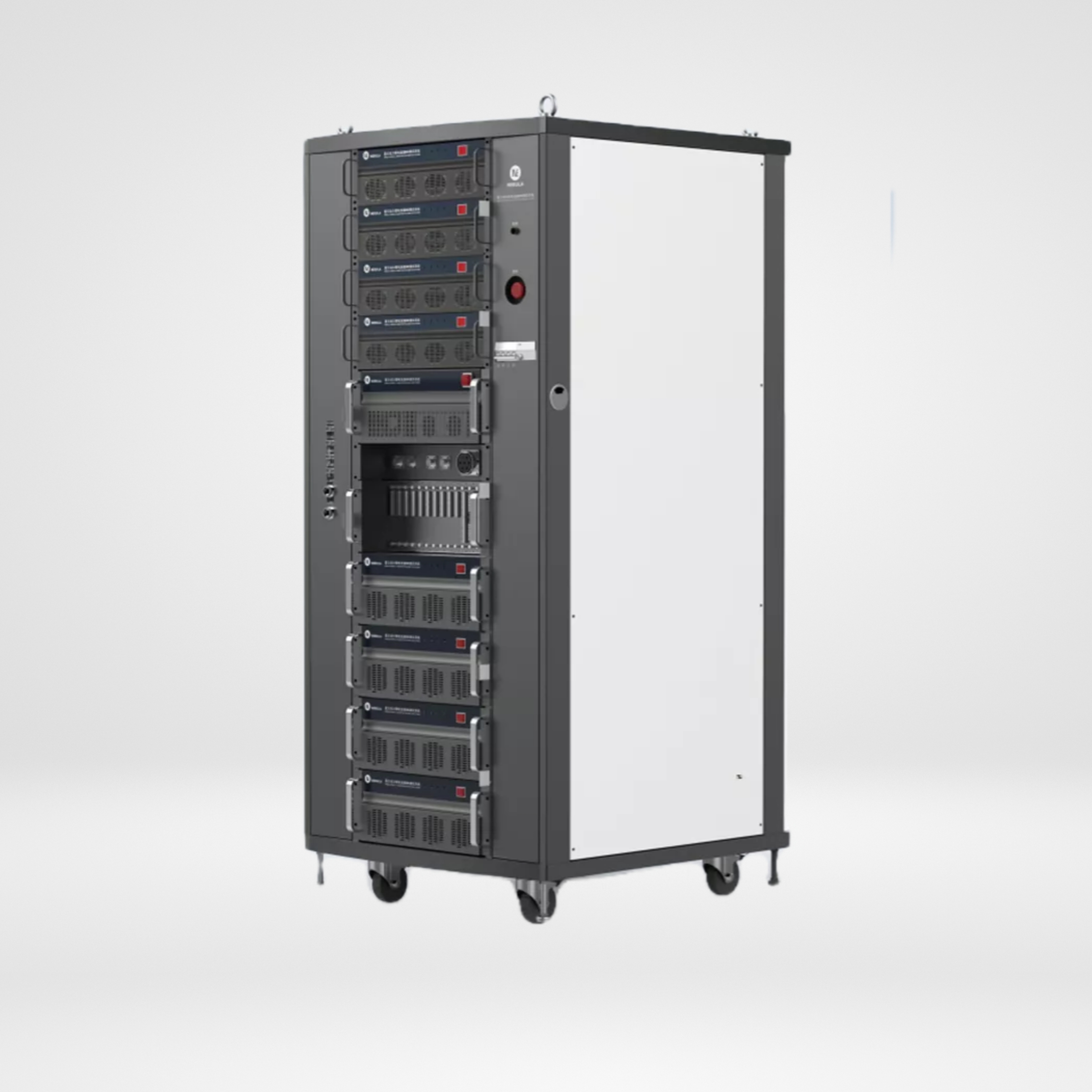
Ess Solution I recently had a chance to talk to Zarko Meseldzija about their process, and some of the other ways the company is helping to create true circularity in lithium-ion battery manufacturing while driving efficiencies to help further decarbonize the manufacturing of new li-ion batteries. You can check it out with the Spotify player, below, or listen on Apple Podcasts, Google Podcasts, or wherever you find podcasts.