In injection molding, material is fed through a hopper into a barrel where a reciprocating screw mixes and melts the material then injects it into a mold.
A well-maintained injection molding machine will improve uptime, decrease cycle time and extend the life of the machine. Bottle Blow Mold
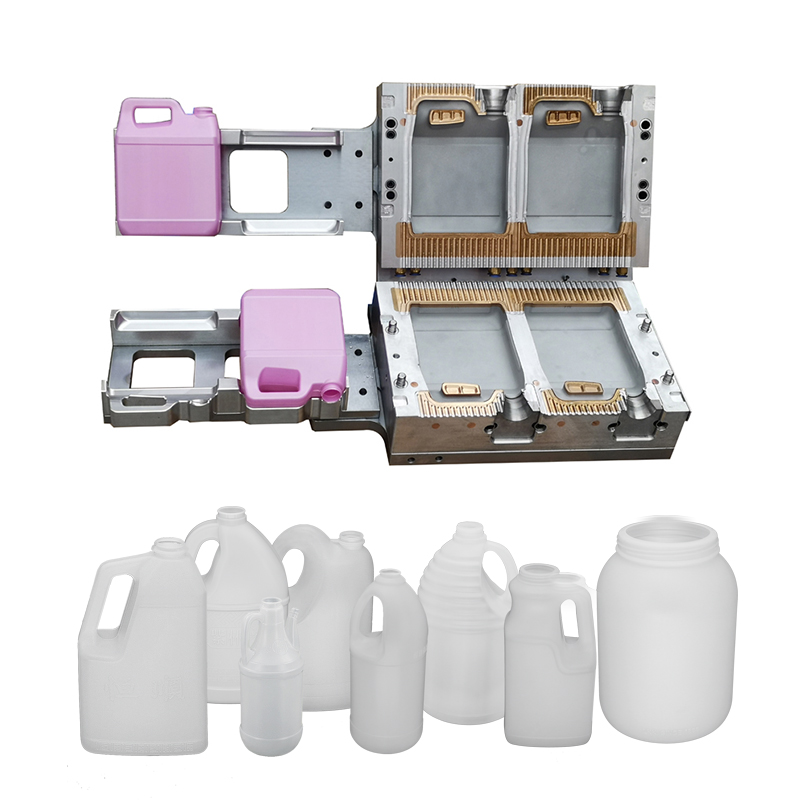
Molders have long used the projected area of the parts and runner to guesstimate how much tonnage is required to mold a part without flash, but there’s a more precise methodology.
Here’s how to get the most out of your stationary mold vents.
Here’s what you need to know to improve the quality of your parts and to protect your molds.
There are many things to consider, and paying attention to the details can help avoid machine downtime and higher maintenance costs, and keep the customer happy.
I conclude this three-part examination of real-world problems and solutions involving hot runners by focusing on heaters, thermocouples, and controls. Part 3 of 3.
AI Integrated Into Injection Molding Process Control
Freeform Injection Molding Eases the Path to Medical Device Product Testing
Arburg Opens Subsidiary in Vietnam
Daimler, OMIC Evaluate Wire-Fed DED for Moldmaking
Ultrasonic Inserts and Heat Staking Kits for Thermoplastics
LS Mtron Opens Division in Mexico
Free, Assisted Data Transfer for Injection Molding Monitoring and Control Platform
Medical Molder, Moldmaker Embraces Continuous Improvement
Metal Injection Molding Line Launches
Melt Temperature Measurement Technology Acquired
Is There a More Accurate Means to Calculate Tonnage?
Cold Deck for LSR Molding
Fakuma 2023: Wittmann Battenfeld Expands All-Electric Line, Direct-Current Capabilities
Internal Gas Pressure Molding Offers Sustainability Benefits
Structural Foam Injection Molding Line Extended
Upgraded Low-Pressure Foam Presses With Elevated Bases
Fakuma: Wittmann Battenfeld to Launch Machine Line at Friedrichshafen Fair
Water Injection Beats Gas Assist in Lightweighting Car Door Panel
Linde Sells Industrial Gas Business to Messer Group
Sumitomo’s Theme: Productivity + Flexibility + Reliability
New Physical Foaming Process for Injection Molding
Lifetime Achievement Awardee Honored For Over 30 Years of Advances in Automotive Molding
Mack Molding Adds ‘Largest Press in New England’
Molder Opts for Machine Flexibility for Complex Jobs
Fakuma 2023: Wittmann Battenfeld Expands All-Electric Line, Direct-Current Capabilities
Video: Ultradent Bags Both Hot Shots Prizes at PTXPO 2023
New Multicomponent Injection Molding Machine Line Launches
Mold, Hot Runner, Digitization and Process Monitoring at K 2022
ZAG Equipment Sales Partners with Portugal’s Plasdan of Portugal
Multicomponent Mold Combines Capping and Unscrewing Functions for Pharma Closure
Dual Injection Units on a Smaller, Electric Press for 2K Medical Molding
Servo-Hydraulic Machine Range Adds Multicomponent Models
Larger Capacity Auxiliary Injection Unit Introduced
Nozzle Shutoff Shuts Down Drool
Cold Deck for LSR Molding
LSR Advances in Dispensing, Tooling and Automation
Fakuma 2023: Wittmann Battenfeld Expands All-Electric Line, Direct-Current Capabilities
New Machine Range Features Adjustable Clamp for Micromolding
Injection Machines Use Novel Two-Stage Molding System
K 2022: LSR Cell Makes Four Different Lids With Each Cycle
Finding a Niche in LSR Tooling
New LSR Cold-Runner Package at K 2022
In-Mold Labeling Applied to Medical
Kurz Opens New Plant in Vietnam
Borealis and Bockatech Showcasing Ultra-Lightweight Reusable PP Cups
New In-Mold Labeling System Launches at K 2022
New In-Mold Labels Enhance Recycling of PP Containers
DuraTech Industries Licenses TactoTek’s Injection Molded Structural Electronics (IMSE)
Packaging Project Combines Thin Walls, Recycled Content and High Speeds
Muller Technology Announces New COO
Get Ideas from IMDA Award Winners In IML, IMD & In-Mold Electronics
Fakuma: Wittmann Battenfeld to Launch Machine Line at Friedrichshafen Fair
New Package Concept Offers Relief from PP Shortages & Soaring Prices
New Machine Range Features Adjustable Clamp for Micromolding
Innovative Micro-Molding From Minnesota Machine Shop
Matrix Tool: Welcome to the Family
X2F and Covestro Collaborate on Innovative In-Mold Electronics for Automotive Lighting
Matrix Tool Wins Inaugural Hot Shots Competition
Fakuma: Wittmann Battenfeld to Launch Machine Line at Friedrichshafen Fair
Westfall Technik Opens Medical Molding Facility
Freudenberg Medical Adds Six Machines
MTD Micro Molding Completes Expansion
Fakuma Show Goes On (Digitally) for Wittmann Battenfeld
Micromolder Makuta Adopts Carbon 3D Printing
K 2019 Preview: Injection Molding Goes for the ‘Green’
IPEX Opens Injection Molding Facility in North Carolina
Adaptive, Automatic Process Control for Injection Molding
Wittmann Finds Battery Partner for Direct Current (DC) Molding Machine Concept
Fakuma 2023: More Details on New Machine Line
Fakuma 2023: New Hybrid Machine Launches
Injection Compression Molding as Alternative to Thermoforming
Fakuma 2023: Wittmann Battenfeld Expands All-Electric Line, Direct-Current Capabilities
Custom Injection Molder Plugs into All Electric Machines
Arburg Marks Anniversary with New Generation of Machines
Compact Hybrid Injection Molding Machine Launched
Word Games: What’s a ‘Hybrid’?
50 Years...600 Issues...and Still Counting
Integrated Injection System for Blood-Collection Tubes
PET Preform Molding Advances on Display
Complete End-to-End PET Preform Production
K 2022: ‘We’ve Been Waiting 40 Years!’
Mold Opaque White PET Bottles – Without Pigment
New Mid-Size PET Preform Machine
Advances in PET Bottle & Cap Molding at Drinktec Show
Expanded PET Preform Molding Machine Line
Injection Molding: Lubricant Coating Keeps PET Preforms Scratch-Free
Injection Molding: PET Preform Molding Machine Switches to Side Entry
How Graham Packaging Counters PCR Supply/Demand Squeeze
Blow Molding: Online PET Preform Inspection Uses AI to ‘Self-Learn’
Plastic injection molding is a cyclical manufacturing process that allows for cost-efficient production of a mass number of identical parts made from either thermoplastic or thermoset materials.
How to Improve Consistency in Injection Molding?
Cushion values in injection molding ultimately are an indication of a part’s quality, especially its dimensions. A consistent cushion will create consistent part dimensions.
How to Get Rid of Bubbles in Injection Molding?
It is important to determine which type of bubble your part has, and what the root cause might be. Determining bubble type will allow you to pinpoint the source and determine your next course of action to eliminate the problem.
How can I improve my injection molding quality and productivity?
Most molders are still relying on “general-purpose” screw designs that go back 30 years. With all of the technical improvements that have been made on machines over that time, nothing has been done to improve melt uniformity. We still use “general-purpose” (GP) screws, which well-known screw designer Bob Dray wisely has called “no-purpose” screws. That is they do not melt plastic uniformly. Processing with a uniformly melted plastic would seem like a high priority, but it has seen little if any attention.
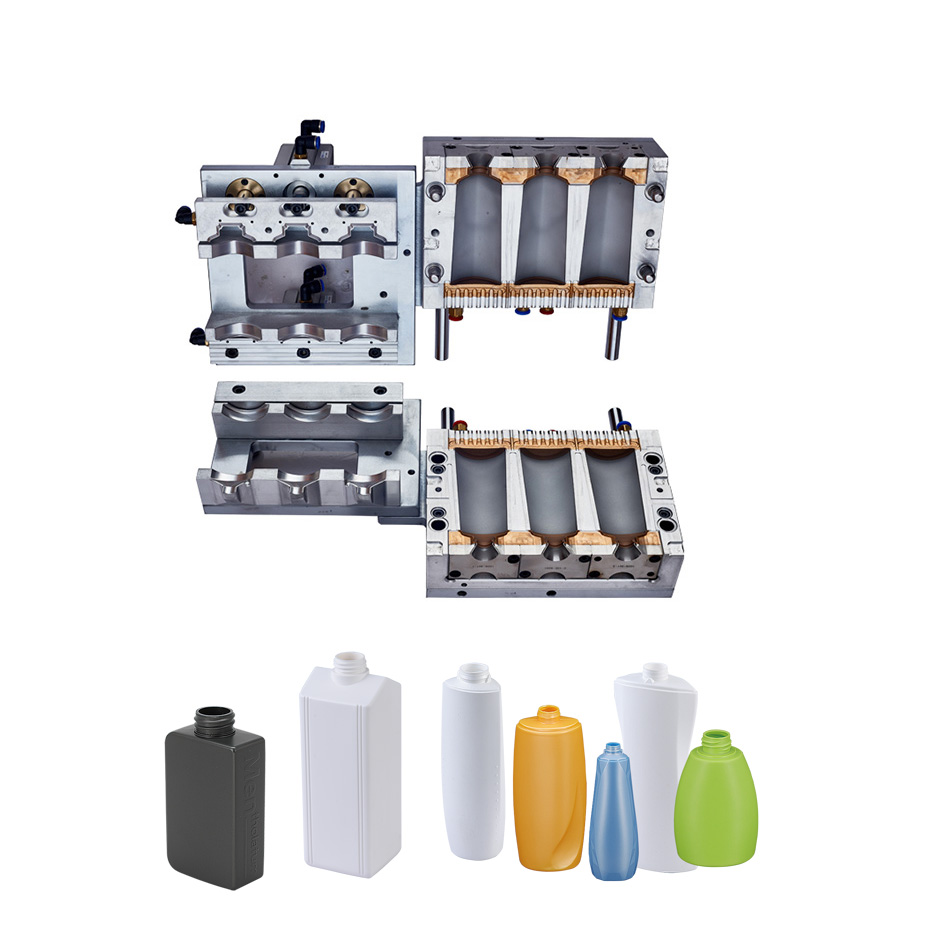
Pet Injection Mold Blowing © 2023 Gardner Business Media, Inc. Privacy Policy [Log On]