One of the most common forms of labeling in the packaging industry involves affixing self-adhesive branding and designation stickers to discrete end units off a spool off said stickers. Though the applications for food and beverage products are most visible, this type of labeling is used in the pharmaceutical, petrochemical, electronics, and home goods industries as well.
Beverage label-maker image: Manuel Ribeiro Tamper Seal Labelling Machine
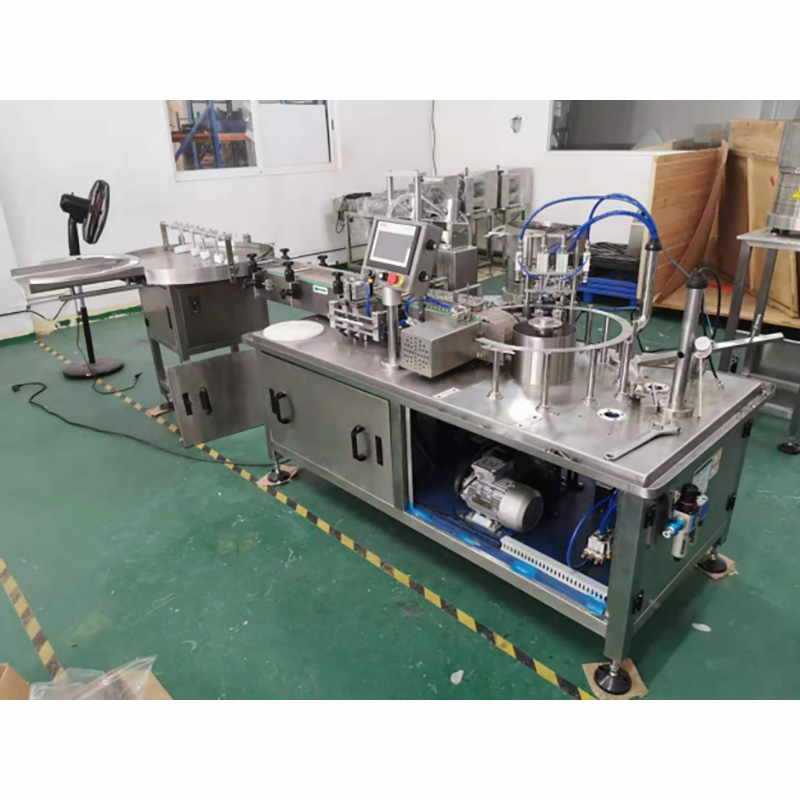
In this spool-based automated labeling operation, discrete products ride on a conveyor into a separating station that evenly spaces them out. Then the products travel onward to the label-station proper. Here, a three wheels work in conjunction to intermittently drag the unwound and peeled back portion of the label spool across product surface … sometimes processing 100 feet per minute or mote of labels.
A belt stops and starts the web to synchronize the labeling-wheel stroke with that of the conveyor upon which the discrete products are riding. Either closed or open-loop control of the label-wheel axle position maintains proper web tension. To ensure straight and centered placement, a machine-vision camera or other sensor reads a mark on each sticker to inform the controls of any slight drive-wheel adjustments required during deceleration and final application.
Automated labeling machine image: Baloncici
Labelers include several coordinated motion axes.
Sizing motion components for this application often requires separate consideration of the label-web feed axle (axis), take-up web-tensioning reel, and spent web backing axle (axis). The forces and speeds as well as the continually changing spool geometries and inertias are primary considerations.
Shown here is a shrink-wrapping station for the packing of beverage bottles. Image: Dedmityay
Vegetable flow-wrapping operations must maintain high throughput.
Stretch wrapping is essential to bundling a wide array of goods into transportable and salable units. Such packing also serves to protect the discrete items in the pack … and simplify distribution. Where consumers will see the shrink wrapping, it must be especially attractive and rugged. In fact, stretch wrapping (thanks to its effectiveness and relative simplicity) has over the last 10 years become the leading choice for unitized goods distribution.
Shrink-wrap machine image courtesy KHS
Of course, some production warehouses employ partially automated approaches. Here, workers affix film to bundle being wrapped and then reach or walk around said bundle multiple times with a wrap bar.
The S-Carriage InstaThread Pre-stretch Film Carriage from Orion Packaging Systems can help packaging facilities save up to 15% on film per load — a substantial savings to help offset the rising cost of film seen over the past year. At the heart of the carriage design are two pre-stretched rollers. Film travels in an S pattern around the rollers, providing over 180° of film contact to reduce slippage and neckdown. The result is a consistent pre-stretch of 260% at different tensions and 1 in. less neckdown.
Elsewhere, a bundle might be manually placed onto a rotating turntable so that an machine executes the rest of the wrapping process. In contrast, fully automated stretch-wrap operations employ conveyors to load and unload bundles into and out of turntable stations that apply, wrap, and cut film off a web at exceptionally high rates. Rotary and linear motion designs (including three-axis gantry systems) complement the core conveyor and machine-vision systems that enable this application.
Motion components are key to PET-bottle molding operations. Image: Africa Rising Agency
For all their environmental drawbacks, plastic bottles do in fact make modern life easier — and are among the plastic packaging items with the highest rates recycling. Most of these bottles are made of the thermoplastic known as polyethylene terephthalate or PET because the material is strong, impermeable, light, attractive, and recyclable. After polymerization processing with techniques to minimize diethylene glycol, the goal during the molding process is to use techniques minimizing residual acetaldehyde.
Heated PET is loaded on a parison tube mold and then cut to length. The parison warms and enters a bottle-shaped mold. Then a mandrel enters the parison to blow pressurized air and stretch the PET to the shape of the mold’s geometry. Molecular polarization, cooling, and finished bottle ejection follow.
Motion components abound in automated PET-bottle manufacturing systems. In some cases, multiple synchronized carriages execute PET-material place functions while a rodless electric actuator executes the insertion and removal strokes of the molding task itself. In fact, highly controllable rodless actuators based on electric-motor operation have come to replace hydraulic cylinders in many PET-bottle manufacturing machines, as rodless actuators can offer faster, simpler, and more efficient operation with less risk of contamination.
Because the global supply chains for recycled food-grade materials is incomplete, some packagers have strived to lightweight their bottles. This reduces the amount of plastic rereleased into the environment and reduces transportation costs. Elsewhere, PET packaging has come to replace other package types. Some involves the use of ThermaSet PET in place of glass; bottle lightweighting with thin-wall variations as well as texturization and vertical banding; hybrid construction with polyolefins; and handless designs. All of these options present unique challenges for the automated machinery that produces them.
Successful inspection and detection in packaging Recipes in the context of HMIs What is a direct drive in the context of motion applications? Dorner’s virtual showcase now open with nine product demonstrations Podcast: Planar motors and linear transfer systems in action (addressing COVID and more)
Lisa Eitel has worked in the motion industry since 2001. Her areas of focus include motors, drives, motion control, power transmission, linear motion, and sensing and feedback technologies. She has a B.S. in Mechanical Engineering and is an inductee of Tau Beta Pi engineering honor society; a member of the Society of Women Engineers; and a judge for the FIRST Robotics Buckeye Regionals. Besides her motioncontroltips.com contributions, she also leads the production of the quarterly motion issues of Design World.
Browse the most current issue of Design World and back issues in an easy to use high quality format. Clip, share and download with the leading design engineering magazine today.
Top global problem solving EE forum covering Microcontrollers, DSP, Networking, Analog and Digital Design, RF, Power Electronics, PCB Routing and much more
The Engineering Exchange is a global educational networking community for engineers. Connect, share, and learn today »
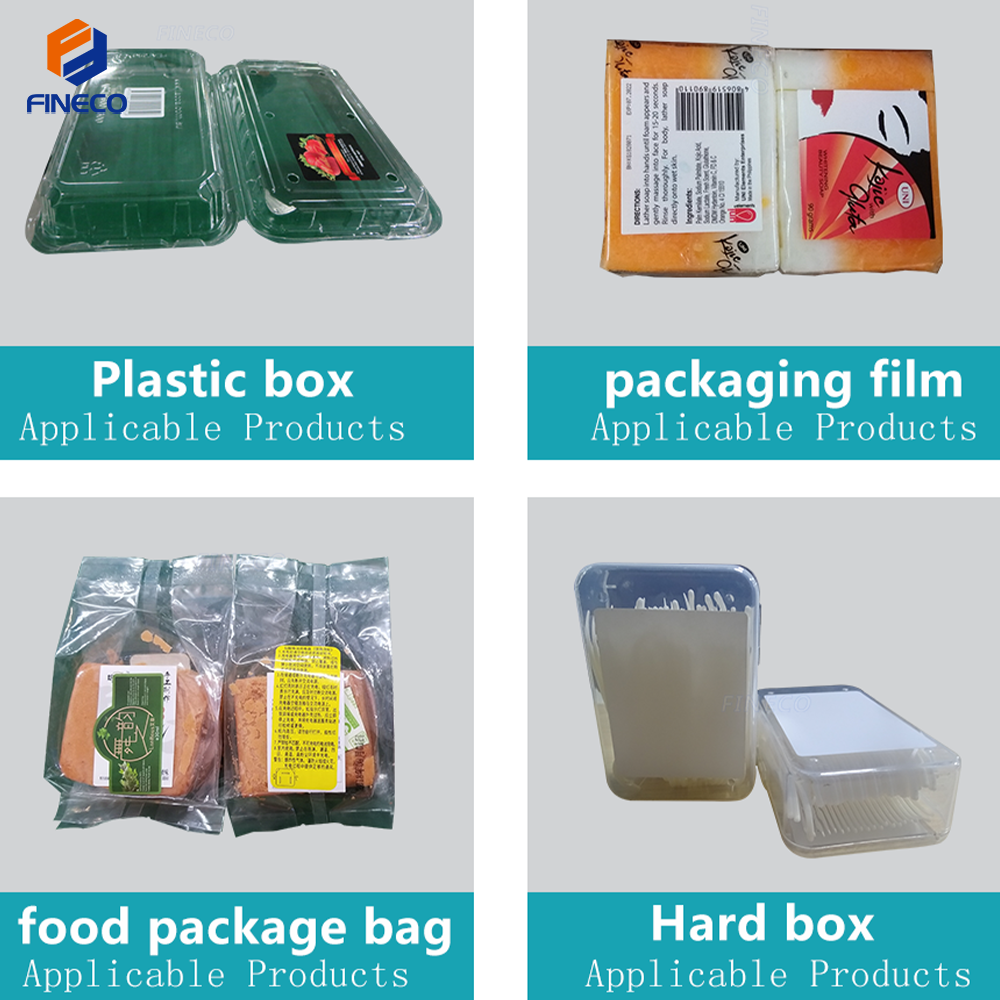
Auto Flat Top And Bottom Surface Labeling Machine Copyright © 2023 WTWH Media LLC. All Rights Reserved. The material on this site may not be reproduced, distributed, transmitted, cached or otherwise used, except with the prior written permission of WTWH Media Privacy Policy | Advertising | About Us